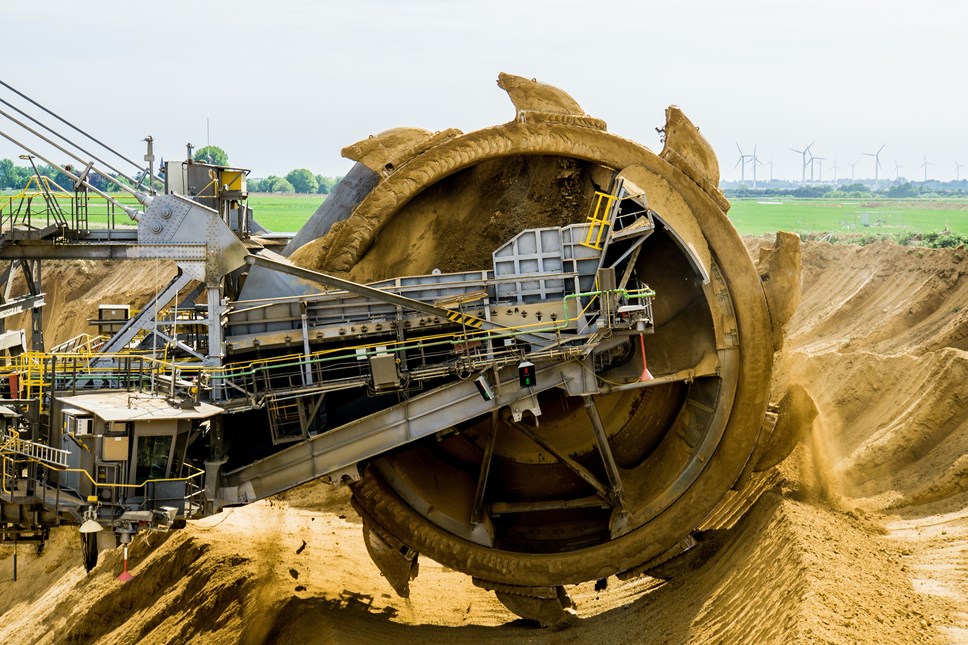
Monday Musing: Green Vehicles…not so green
Glenn Dives, Corporate & Public Affairs Officer visited the Natural History Museum and discovered some very rare metals
A few weeks ago, I went to a talk at the Natural History Museum, the talk was titled ‘We need to talk about Green Energy’. Given our work and that of our members in this area, I thought it would be interesting. Contrary to what you may be expecting it was not about the urgent need for renewable energy or the damage of continued global warming, rather it was centred upon the practicalities and realities of switching to cleaner technologies. (For clarity I am will ignore the issue of CO2 Emissions and climate change and concentrate on the issue of resource production).
The talk was delivered by Dr Robin Armstrong, who outlined the profound resource implications in a very direct and matter of fact way of switching to Electric Vehicles (EV) and Green Energy (GE). While this article is primarily focusing on EV it has lessons for the wider clean technology debate but first, let’s talk about mining.
The world’s largest copper mine by production, is called Escondida in Chile. The mine pit has a depth of 645 meters, while its external dimensions are 3.9 km by 2.7 km or 10 square kilometres!! That’s most of central London. It is places like this that the natural resources for EVs come from.
The Resources
Current government policy is to transition to a zero-emission vehicle fleet by 2050 which may even be brought forward, depending on future political or environmental pressures. That fleet, much like today’s, is going to be made of metal. But not just good old-fashioned steel, no, they are going to be made of some pretty unusual metals.
- Copper (ok not so unusual)
- Cobalt (I remember that one from school)
- Lithium (batteries, right?)
- Neodymium (Star Trek?)
- Dysprosium (That’s made up)
No, the last two were not made up. They are two of the so-called rare-earth metals, named because until relatively recently they were not well known and had no real practical uses. Today however, these metals are increasingly used to make lightweight permanent magnets for electric motors. Neodymium alloys for example are used to make the strongest magnets in the world[1], vital for the operation of EVs, but that is only the beginning. EVs not only need unusual metals, they also use a range of metals far more intensively then-current vehicles. For example, copper, according to Mining Technology.com, “a typical EV contains 10 times more copper than a conventional vehicle.”[2] For example conventional car uses between 8-22 kilos (18-49 lbs), while an EV 83 kilos (183 lbs)[3].
The production of these resources is not straight forward, they involve a huge amount of work to extract and process, which has consequences. Neodymium is often found in ores alongside the radioactive element Thorium, which is then separated out as a by-product of the refinement process. This has potential health effects for the workers at the mine if safety procedures aren’t followed[4].
With that in mind here are some numbers; to replace all 31.5 million cars on the UK roads with EVs (not including LGV and HGV fleets) by 2050, assuming they use the most resource-frugal next-generation batteries, would take:
- 207,900 tonnes cobalt, (just below 2x total current world production)
- 264,600 tonnes of lithium carbonate (LCE), (that’s ¾ of the world’s lithium production)
- at least 7,200 tonnes of neodymium and dysprosium (nearly the entire world production of Neodymium)
- 2,362,500 tonnes copper (half of the world’s copper production during 2018)[5]
Even ensuring the annual supply of EVs only, from 2035 as pledged, will require the UK to annually import the equivalent of the entire annual cobalt needs of Europe. We are going to need more mines!
Mining is just the beginning
Then there are the production costs. Cobalt requires roughly 7,000-8,000 kilowatt-hours of power for every tonne of metal produced and copper, 9,000-kilowatt-hours per tonne. For the rare earth metals, it is roughly 3,350-kilowatt-hours per tonne. So, after some quick maths (thank you Natural History Museum) replacing all 31.5 million cars would require 22.5 terawatt-hours of power to produce the new metals for the UK fleet, amounting to 6% of the UK's current annual electrical usage. On the global scale with an estimated two billion cars worldwide, the energy demand for extracting and processing the metals is almost four times the total annual UK electrical output.[6]
Then there are the ongoing power needs for EVs. The Natural History museums experts have analysed the published figures for some current EVs based on current usage. According to their calculations, replacing all the 31.5 million cars would use at least 63 terawatt-hours of power, meaning a 20% increase in UK generated electricity.[7]
For clarity, it is worth noting that a conventional internal combustion engine car needs less energy to produce than any electric car because it has far less variety of metals in it, as well less metal to begin with. This means the additional energy costs associated with extracting and producing them are not there. However, it is still pretty energy-intensive as all cars are still made of steel and aluminium which are extremely energy-intensive. For example, total car production in the EU in 2018 require 389 terawatt per year. Now that was a decrease of 10.8% since 2005, with each car on average requiring 2.3 MWh, a 16.9% reduction over the same period[8].
That then leads on to questions of energy generation, so let’s look at GE. If we used wind farms to generate the power for the projected two billion cars in the world (and assuming average usage similar to the UK's), we would need the equivalent of a further years’ worth of total global copper supply and 10 years’ worth of global neodymium and dysprosium production to build the wind farms. Those wind farms have electric motors as well (larger versions of the ones in EVs) and there are similar issues for solar panels.
So, what do we do?
When set out in this way, the task appears mind-boggling, even impossible and there are no easy answers. There are costs associated with anything and everything we do. What is essential is that these facts become more widely known. This will ensure we stand a chance of being able to find solutions to the challenges and approach things in a smarter and more informed way. As a sector I know we are already a part of that discussion and we certainly can play a larger role in shaping the future.
References
[1] Handbook of Modern Sensors: Physics, Designs, and Applications, 4th Ed. USA: Springer. p. 73. Fraden, Jacob (2010). ISBN 978-1441964656. And "What are neodymium magnets?". wiseGEEK website. Conjecture Corp. 2011. Retrieved October 12, 2012.
[2]Electric vehicle revolution to drive copper demand, Mining Technology.com https://www.mining-technology.com/comment/electric-vehicle-revolution-drive-copper-demand/, Published 12 December 2017
[3] Nicholas LePan How Much Copper is in an Electric Vehicle? https://www.visualcapitalist.com/how-much-copper-is-in-an-electric-vehicle/ Published November 13, 2018
[4] Sofia Sanchez Manzanaro & Marta Rodriguez ‘Why electric cars aren’t as environmentally-friendly as you think’ Euronews, https://www.euronews.com/2019/08/17/exporting-contamination-who-pays-the-environmental-cost-of-electric-car-production last updated: 19 August 2019
[5] K Pavid, ‘We need more scarce metals and elements to reach the UK's greenhouse gas goals’, Natural History Museum, https://www.nhm.ac.uk/discover/news/2019/june/we-need-more-metals-and-elements-reach-uks-greenhouse-goals.html, published July 2019
[6] Pravid, ‘We need more’ https://www.nhm.ac.uk/discover/news/2019/june/we-need-more-metals-and-elements-reach-uks-greenhouse-goals.html, published July 2019
[7]Pravid, ‘We need more’ https://www.nhm.ac.uk/discover/news/2019/june/we-need-more-metals-and-elements-reach-uks-greenhouse-goals.html, published July 2019
[8] Resource-efficient production, European Automobile Manufacturers Association https://www.acea.be/statistics/tag/category/resource-efficient-production-trends